Porosity in Welding: Identifying Common Issues and Implementing Finest Practices for Prevention
Porosity in welding is a prevalent problem that frequently goes unnoticed till it triggers significant troubles with the stability of welds. In this conversation, we will certainly discover the vital elements contributing to porosity development, examine its detrimental impacts on weld performance, and go over the ideal methods that can be adopted to lessen porosity occurrence in welding procedures.
Typical Causes of Porosity
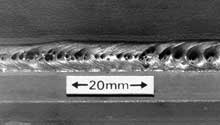
An additional regular culprit behind porosity is the existence of impurities on the surface of the base steel, such as oil, grease, or corrosion. When these contaminants are not successfully gotten rid of before welding, they can evaporate and become entraped in the weld, triggering issues. Making use of filthy or wet filler products can present impurities right into the weld, adding to porosity issues. To alleviate these usual sources of porosity, complete cleansing of base metals, proper protecting gas selection, and adherence to ideal welding criteria are vital techniques in accomplishing high-grade, porosity-free welds.
Effect of Porosity on Weld High Quality

The visibility of porosity in welding can significantly endanger the architectural stability and mechanical residential properties of welded joints. Porosity creates voids within the weld steel, deteriorating its general strength and load-bearing capacity.
Welds with high porosity degrees often tend to display reduced effect toughness and decreased capacity to deform plastically prior to fracturing. Porosity can impede the weld's capability to properly transfer pressures, leading to premature weld failure and possible safety dangers in essential frameworks.
Ideal Practices for Porosity Prevention
To improve the architectural integrity and high quality of bonded joints, what particular procedures can be implemented to reduce the event of porosity throughout the welding process? Porosity prevention in welding is vital to ensure the stability and toughness of the final weld. One efficient method appertains cleaning of the base metal, eliminating any kind of impurities such as rust, oil, paint, or wetness that might cause gas entrapment. Making sure that the welding tools is in good condition, with clean consumables and proper gas circulation prices, can additionally significantly decrease porosity. Furthermore, keeping a secure arc and regulating see this the welding parameters, such as voltage, present, and take a trip rate, helps produce a regular weld swimming pool that decreases the threat of gas entrapment. Using the correct welding technique for the specific material being welded, such as adjusting the welding angle and gun position, can better prevent porosity. Regular inspection of welds and immediate remediation of any issues identified during the welding process are crucial techniques to prevent porosity and produce top quality welds.
Importance of Correct Welding Methods
Executing appropriate welding strategies is paramount in making sure the architectural integrity and top quality of bonded joints, building on the foundation of effective porosity avoidance steps. Welding techniques straight impact the total strength and durability of the bonded structure. One crucial aspect of correct welding techniques is keeping the proper warm input. Excessive warmth can result in boosted porosity as a result of the entrapment of gases in the weld swimming pool. Conversely, inadequate heat may cause incomplete blend, creating possible weak points in the joint. Furthermore, using the suitable welding criteria, such as voltage, current, and take a trip rate, is important for attaining sound welds with marginal porosity.
Additionally, the option of welding procedure, whether it be MIG, TIG, or stick welding, need to straighten with the specific requirements of the job page to make certain optimum results. Correct cleaning and prep work of the base metal, in addition to choosing the right filler product, are likewise important parts of efficient welding techniques. By adhering to these ideal techniques, welders can reduce the threat of porosity development and produce top notch, structurally audio welds.
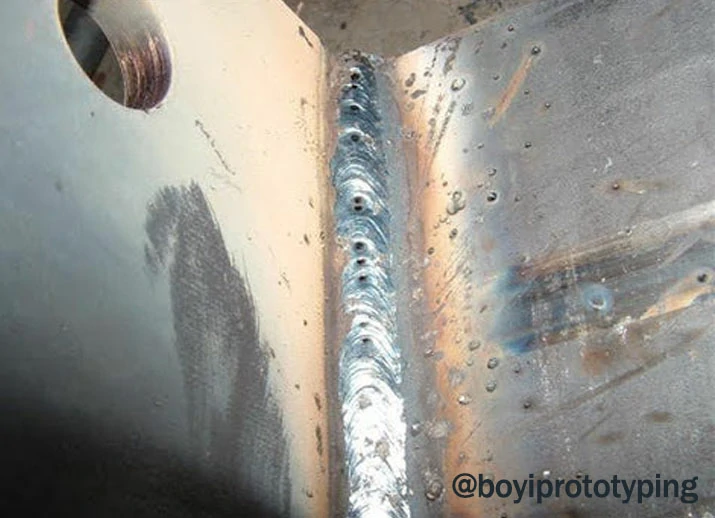
Checking and Top Quality Control Actions
Checking treatments are necessary to find and protect against porosity in welding, making certain the toughness and toughness of the final item. Non-destructive screening approaches such as ultrasonic testing, radiographic testing, and visual examination are generally used to determine prospective defects like porosity.
Post-weld inspections, on the other hand, examine the last weld for any flaws, consisting of porosity, and confirm that it meets defined standards. Executing a thorough quality control strategy that consists of thorough testing treatments and inspections is critical to lowering porosity issues and ensuring the general quality of welded joints.
Final Thought
To conclude, porosity in welding can be a typical problem that affects the top quality of welds. By recognizing the common reasons for porosity and carrying out ideal techniques for prevention, such as appropriate welding methods and screening actions, welders can ensure top quality and reputable welds. It is necessary to focus on avoidance methods see this website to minimize the occurrence of porosity and maintain the integrity of welded structures.